¿Cómo cambiarán las estrategias de suministro en México después de la pandemia?
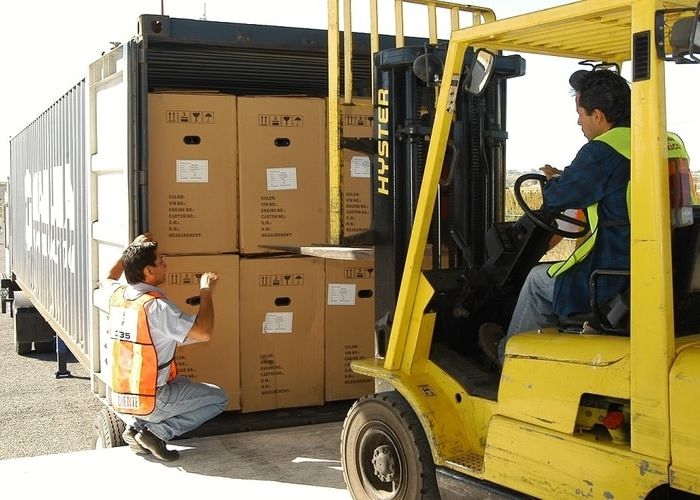
Tras la pandemia las estrategias de suministro de empresas mexicanas contemplarán la cercanía con proveedores, mayor almacenamiento y más flexibilidad.
Previo a la pandemia, muchas compañías en México habían adoptado una filosofía de suministro bajo el concepto Just-In-Time, que Deloitte define como solicitar solo los materiales y componentes necesarios para la operación de la organización en el momento que se requieren. La idea es reducir, en la medida de lo posible, el gasto en almacenamiento. Trabajar únicamente con lo que necesita la empresa en el momento también permite una agilidad mayor en procesos de transformación y adaptación productiva.
Es poco probable que, una vez terminada la crisis sanitaria, las empresas regresen a este modelo. “Todas estas metodologías desaparecerán o deberán adecuarse. Las empresas se dieron cuenta que había aspectos que no se consideraban para mantener a flote los negocios. Y uno de ellos era justamente prevenir y prepararse para factores extremos. Había mucha atención en elementos macroeconómicos y de demanda, pero no había estrategias de continuidad de negocio”, apunta Cristian Fraga Lagos, Business Owner de la firma de certificación Círculo de Proveedores.
Pero no es solo que las empresas no tuvieran planes claros para sobrellevar eventos imposibles de prever, como una crisis sanitaria. Tampoco había una evaluación precisa de qué tan sólida era su operación en el día a día.
“Nos dimos cuenta de la falta de visibilidad que tenemos dentro de nuestra propia cadena de suministro. Tenemos muy cercanos a [nuestros proveedores] nivel dos, nivel tres. Pero cuando nos vamos más atrás, al proveedor de mi proveedor en Asia o Europa […], la capacidad de vigilancia [era insuficiente]”, apunta Carlos Zegarra, socio líder de Management Consulting de PwC México, refiriéndose a la situación del sector automotriz en México.
Estos dos problemas no aplican solo al país, ni solo a algunos sectores. De acuerdo con una encuesta realizada por McKinsey desde los primeros días de la pandemia, el 73% de los líderes de las cadenas de suministro a nivel global se encontraron con problemas en su base de proveedores a raíz de la pandemia y 75% enfrentaron retos de producción y distribución; lo que indica fallas generalizadas de escala global.
Para el caso específico de México, se espera que estas disrupciones lleven a que las estrategias de suministro de las empresas transiten hacia una relación más cercana entre los proveedores y sus clientes.
“La consolidación de proveedores puede minimizar riesgos […]. Diversificar el número de opciones sigue siendo importante, pero es crucial pensar con quiénes se establecen lazos. Buscar empresas con las que se pueda contar si alguna de ellas llega a tener un contratiempo […]. Y al reducir la plantilla de aliados comerciales, pueden crearse mejores estrategias de suministro para las dos partes”, señala Cristian Fraga Lagos.
También será necesario invertir más que antes en estrategias de almacenamiento, desplazando en gran medida al modelo Just-In-Time. Esta tendencia es tan fuerte que ya se está observando un incremento sustancial en la actividad económica ligada a la construcción de naves industriales, particularmente al norte del país y en la zona del Bajío, donde está la masa más numerosa de compañías de manufactura y maquila en México.
Sin embargo, no debe quedar todo del lado de los proveedores o de la estrategia logística. Según Carlos Zegarra, en industrias como la automotriz también se están empezando a considerar cambios radicales en la operación de las compañías y hacerlas más ágiles. Aquí, la idea ya no es asegurar un buen suministro de materiales y componentes, sino darle continuidad a las actividades aún en medio de una disrupción imposible de evitar.
“[La cuestión será] qué tan ágil soy, como empresa, para adaptar mi capacidad productiva actual a los cambios en la cadena de suministro […]. Por ejemplo, cambiar mis flujos productivos para fabricar unidades menos complejas, o que requieran otro tipo de componentes. O bien desarrollar un Plan B con componentes pre-aprobados, con el que si me falla el suministro del componente A, no me sea difícil usar un componente B pre-aprobado, que me genere un resultado no tan diferente"
"Aquí, el nombre de juego será la resiliencia”, afirma Zegarra.